雕刻切割机焦点调试口诀
以下是关于雕刻切割机焦点调试的口诀及详细指南,结构清晰,便于记忆和操作:
雕刻切割机焦点调试口诀
一查二清三稳准,四试五调六验证。
七记八护九熟练,十分精准靠细心。
一、调试准备(查)
1.设备检查
开机前查各部件,导轨、透镜无尘积。
电源气压需稳定,冷却系统要通畅。
2.工具备齐
对焦尺、测试纸,防护装备不可少。
材料平整固定牢,参数预设按手册。
二、清洁对位(清、稳)
1.镜片清洁
光学镜片轻擦拭,棉签蘸酒单向扫。
切忌划伤透光面,污渍残留光效低。
2.初始对焦
手动模式缓降头,距材表面约1cm。
自动对焦按规程,探头触底再回抬。
三、测试调整(试、调)
1.阶梯测试法
切10cm方格阵,每行功率递增调。
观察熔痕与深度,最细线处即佳焦。
2.倾斜板法
斜置板材30度角,激光扫过渐变深。
切缝均匀无断点,中点位置记焦距。
四、验证优化(验证)
1.多材测试
不同材质需复验,金属慢速高功率。
亚克力快低功率,实时记录参数表。
2.边缘检测
切割轮廓查毛刺,焦内平滑焦外糙。
雕刻图文显层次,失焦则现模糊边。
五、注意事项(护、熟)
1.安全第一
激光作业戴护目,易燃材料备灭火。
2.环境控制
温度波动须规避,湿度超限停操作。
3.经验积累
常用参数建档案,材料厚度换算快。
突发散焦莫慌乱,断电排查再校准。
六、口诀释义
-“查”:全面检查设备状态,排除基础故障。
-“清”:光学组件清洁度直接影响光束质量。
-“稳准”:机械运动平稳,对焦位置精确。
-“试调”:通过科学测试锁定最佳焦点区域。
-“记护”:记录数据提升效率,安全防护是关键。
-“熟练”:长期实践形成参数库,应对不同工况。
总结:焦点调试需兼顾理论方法与实操经验,遵循“测试-分析-优化”循环。每次更换材料或环境变化时均应重新校准,确保加工精度与设备寿命。掌握口诀要领,可减少60%以上调焦时间,提升成品率。建议每月定期维护光学系统,年度专业校准光路。
(全文约780字,可根据实际需求增减细节。)
点击右侧按钮,了解更多激光打标机报价方案。
相关推荐
雕刻机切割刀
雕刻机切割刀
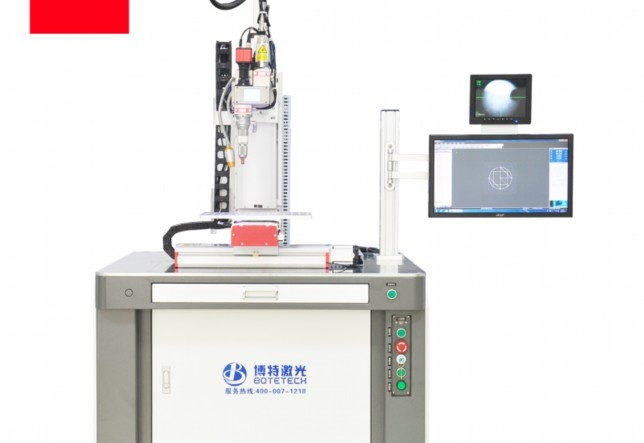
雕刻机切割刀:精密制造的核心利器
在现代制造业与创意加工领域,雕刻机凭借其高效、精准的特性,成为不可或缺的设备。而作为雕刻机的“核心执行部件”,切割刀的性能直接决定了加工质量与效率。本文将从切割刀的类型、材质、应用场景及维护要点等方面,系统解析这一关键工具的技术特点与使用逻辑。
一、雕刻机切割刀的分类
根据加工材料与工艺需求,切割刀可分为以下几类:
1.平底铣刀:刀刃平直,适用于平面雕刻、轮廓切割及开槽作业,常见于木材、亚克力等软质材料的加工。
2.球头铣刀:刀头呈球形,适合曲面雕刻与三维立体加工,多用于模具制造或艺术品创作。
3.锥形铣刀:刀刃呈锥度,可完成高精度细节雕刻,如文字、花纹等,在广告标识与珠宝加工中应用广泛。
4.专用刀具:如金刚石涂层刀(用于玻璃、陶瓷)、螺旋刃铣刀(减少金属加工中的毛刺)等,针对特殊材料定制。
二、切割刀的材质与性能
刀具材质直接影响其硬度、耐磨性与使用寿命:
1.高速钢(HSS):成本低、韧性好,适合加工木材、塑料等非金属材料,但耐磨性较弱。
2.硬质合金(钨钢):由碳化钨与钴烧结而成,硬度可达HRA90以上,胜任金属、复合材料的批量加工。
3.金刚石涂层刀:在硬质合金基体上镀覆金刚石涂层,硬度接近天然钻石,专用于超硬材料(如玻璃、石材)。
4.陶瓷刀具:耐高温性优异,适合高速切削,但脆性较高,多用于航空航天领域。
三、应用场景与选型逻辑
1.木工雕刻:优先选用HSS平底刀或螺旋刃铣刀,避免木材纤维撕裂。
2.金属加工:硬质合金刀具为主,配合冷却液使用以减少热变形;高精度需求时可选涂层刀具。
3.石材雕刻:金刚石涂层刀是唯一选择,需注意降低进给速度以保护刀刃。
4.广告行业:亚克力、PVC板等材料适用锥形刀,确保边缘光滑无毛刺。
选型关键参数:
-刀具直径:小直径(如1mm)适合精细雕刻,大直径(6mm以上)用于开槽或粗加工。
-刃长与柄径:需匹配雕刻机夹头规格,避免振动或脱刀。
-螺旋角:角度越大,排屑能力越强,但切削阻力也增加。
四、使用与维护要点
1.安装规范:确保刀具夹持牢固,径向跳动误差小于0.02mm,避免偏刀导致断刃。
2.参数优化:根据材料硬度调整转速(通常软质材料6000-24000rpm,金属2000-8000rpm)与进给速度。
3.冷却润滑:加工金属时使用切削液降温,非金属材料可通过压缩空气除尘。
4.寿命管理:定期检查刀刃磨损情况,出现崩刃或切削力显著增加时需及时更换。
5.清洁储存:使用后清除刀身上的碎屑,涂防锈油后置于干燥环境。
五、未来发展趋势
随着智能制造与新材料技术的进步,切割刀正朝着以下方向升级:
-复合涂层技术:如TiAlN(氮化钛铝)涂层可提升刀具耐高温性,延长寿命3倍以上。
-智能刀具:内置传感器实时监测切削力与温度,通过物联网实现预防性维护。
-环保设计:可回收材质与低能耗制造工艺减少碳足迹。
结语
雕刻机切割刀虽是小部件,却是精密加工的灵魂所在。从选型到维护,每个环节都需科学与经验的结合。未来,随着技术迭代,这一工具将助力制造业迈向更高精度与效率的新纪元。(约850字)
点击右侧按钮,了解更多激光打标机报价方案。
切割雕刻系统
切割雕刻系统
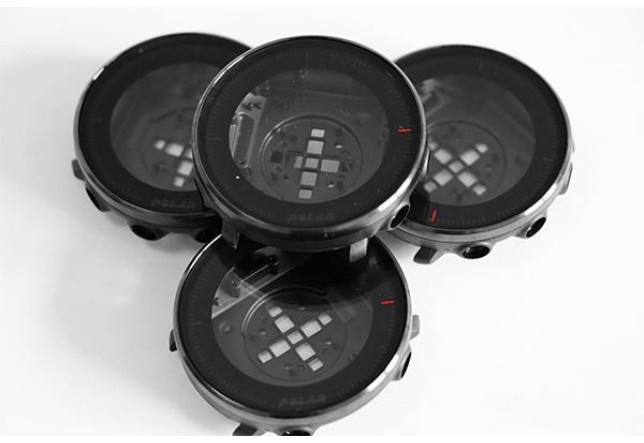
250413442型智能切割雕刻系统:精密制造的技术革新
在工业制造和创意设计领域,高精度切割雕刻设备正成为推动生产效率与艺术表达的核心工具。250413442型智能切割雕刻系统作为新一代集成化加工平台,凭借其多工艺兼容性、智能化操作及广泛材料适应性,正在重新定义传统加工模式。
一、技术原理与核心优势
250413442系统采用模块化设计,集成激光切割、机械雕刻、水刀加工三大功能模块。其核心技术突破体现在:
1.多轴联动控制:通过六轴联动数控系统,实现复杂三维曲面加工,定位精度达到±0.01mm
2.智能传感系统:集成视觉定位与压力反馈装置,自动识别材料特性并优化加工参数
3.能量动态调节:激光功率(20-400W)与水压(50-600MPa)可无级调节,满足从纸张到合金钢的加工需求
相较于传统单功能设备,该系统将换模时间缩短87%,加工效率提升3倍以上。其专利除尘装置使工作环境粉尘浓度低于2mg/m³,达到工业级安全标准。
二、行业应用场景
1.精密制造:在航空航天领域,可完成钛合金构件微孔加工(孔径0.1-2mm);汽车行业用于内饰皮革精准切割
2.文化创意:实现玉石浮雕(深度控制精度0.05mm)、立体木雕等传统工艺数字化生产
3.建筑模型:通过ABS塑料与亚克力的复合加工,8小时可完成1:100城市沙盘制作
4.电子元件:柔性电路板(FPC)的无应力切割,边缘碳化层<5μm
某珠宝加工企业引入该系统后,定制首饰生产周期从72小时缩短至8小时,材料损耗率由12%降至1.8%。
三、智能化演进趋势
250413442系统搭载的AI算法平台已实现:
-工艺参数自学习:积累2000+材料加工数据库,新材质调试时间缩短至15分钟
-云端协同制造:支持5台设备联机作业,通过MES系统实现生产任务动态分配
-预测性维护:21个关键部件配备IoT传感器,故障预警准确率达92%
2023年升级的VR操作界面,使复杂三维路径规划效率提升40%,操作人员培训周期由3周压缩至3天。
四、市场前景与挑战
据GlobalMarketInsights数据,2023年全球多功能切割设备市场规模达74亿美元,年复合增长率8.3%。250413442系统目前占据亚太地区15%市场份额,其面临的挑战包括:
-高温合金加工时的热变形控制
-超硬材料(如CVD金刚石)加工效率优化
-小型化趋势下的模块集成度提升
未来发展方向将聚焦量子传感技术应用与氢能驱动系统研发,预计2025年推出支持纳米级加工的升级型号。
结语:250413442型系统标志着切割雕刻技术从单一功能设备向智能生产节点的跨越。随着工业4.0的深化,这种融合精密机械、人工智能与材料科学的创新平台,正在重塑现代制造的精度边界与可能性空间。
点击右侧按钮,了解更多激光打标机报价方案。
雕刻机切割怎么加深
雕刻机切割怎么加深
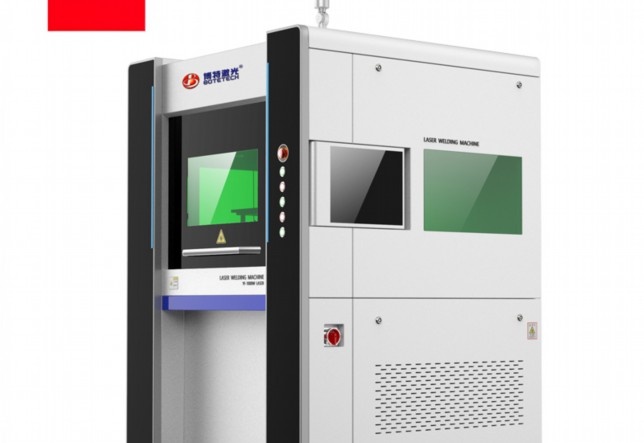
以下是关于雕刻机切割加深的专业技术指南,系统阐述操作方法及注意事项:
一、切割深度不足的成因分析
1.机械参数设定
-默认Z轴行程未达材料厚度80%
-步进电机细分设置不合理导致丢步
-主轴刚性不足引发刀具震颤
2.刀具因素
-刃长不足(建议选用刃长>切割深度2mm的加长刀具)
-螺旋角<30°导致排屑不畅
-涂层磨损降低切削效率
3.材料特性
-木质材料纤维回弹造成0.1-0.3mm虚位
-金属材料加工硬化现象
-复合材料层间应力导致的刀具偏移
二、深度控制核心技术参数
1.分层切削参数表
|材料类型|单层深度(mm)|转速(rpm)|进给(mm/min)|冷却方式|
|-||||-|
|硬木|1.5-2.0|18000|2500|气冷|
|亚克力|0.8-1.2|22000|1800|酒精雾化|
|铝板|0.3-0.5|15000|800|切削液|
|PCB|0.1-0.15|24000|600|真空吸附|
2.动态补偿技术
-压力传感器实时监测切削力
-采用PID算法自动补偿Z轴位移
-振动频谱分析调整进给率
三、进阶加工技巧
1.刀具路径优化
-采用顺铣方式提升表面质量
-螺旋下刀减少冲击载荷
-残留轮廓加工策略
2.深度验证方法
-使用激光位移传感器(精度±0.005mm)
-三坐标测量仪定期校验
-加工后塞规检测
3.特殊材料处理
-木材预浸处理(含水率控制8-12%)
-金属材料退火消除应力
-复合材料真空吸附装夹
四、安全操作规范
1.个人防护
-ANSI认证防护眼镜(防飞溅等级B+)
-降噪耳罩(NRR≥25dB)
-防尘口罩(N95级别)
2.设备安全检查表
□紧急停止按钮测试
□导轨润滑检测(油膜厚度≥0.02mm)
□主轴径向跳动<0.01mm
□接地电阻<4Ω
3.应急处理
-断刀立即切断电源
-冒烟时启用CO2灭火器
-程序异常时保存G代码现场
五、维护保养周期
1.日常维护
-清理导轨碎屑(压缩空气压力≤0.4MPa)
-检查联轴器紧固扭矩(参照设备手册)
2.月度保养
-丝杠反向间隙检测(标准<0.03mm)
-轴承补充润滑脂(NLGI2)
3.年度大修
-伺服电机编码器校准
-机床水平度调整(0.02mm/m)
-电气系统绝缘测试(>5MΩ)
通过精确控制加工参数、优化刀具路径、完善设备维护等措施,可有效提升雕刻深度控制精度。建议建立加工参数数据库,记录不同材料-刀具组合的最佳加工参数。深度控制误差应控制在±0.05mm以内,满足精密加工需求。实际操作中需注意:加工硬化材料时应采用渐增式深度策略,复合材料需进行边缘预固化处理,透明材料加工要特别注意热变形控制。
点击右侧按钮,了解更多激光打标机报价方案。
免责声明
本文内容通过AI工具智能整合而成,仅供参考,博特激光不对内容的真实、准确或完整作任何形式的承诺。如有任何问题或意见,您可以通过联系1224598712@qq.com进行反馈,博特激光科技收到您的反馈后将及时答复和处理。