激光焊接机速度慢如何调快
激光焊接机速度慢的调优方法及注意事项
激光焊接机作为精密加工设备,其焊接速度直接影响生产效率和加工质量。针对设备速度慢的问题,需从设备参数、工艺设置、机械系统等维度进行全面优化。以下是系统化的解决方案:
一、核心参数优化
1. 激光功率提升
(1)核查激光器实际输出功率是否衰减,通过功率计检测实际输出值
(2)在设备允许范围内逐步提升功率(建议每次增幅不超过10%)
(3)功率与速度的匹配公式:V=KP/(D·T),其中V为速度,P为功率,D为材料密度,T为厚度,K为修正系数
2. 波形参数调整
(1)脉冲频率:铝材建议15-25kHz,钢材20-30kHz
(2)脉宽调节:薄板材料采用0.5-2ms,厚板可延长至4-6ms
(3)占空比控制在30-70%范围内,高反材料取低值
二、光学系统优化
1. 光路校准
(1)每周进行光路同轴度检测,偏差需控制在±0.05mm内
(2)使用红光定位系统验证焦点位置
(3)聚焦镜焦距选择:薄板(<2mm)用100-150mm,中厚板(2-5mm)用150-250mm
2. 镜片维护
(1)建立每日清洁制度,使用专用无尘布和光学清洁剂
(2)反射镜每工作8小时旋转45°,延长使用寿命
(3)定期检测镜片透光率,低于90%立即更换
三、机械运动系统优化
1. 运动参数设置
(1)XY轴速度可提升至设备最大值的80%(保留安全余量)
(2)加速度设置为最大值的60-70%
(3)采用S形加减速算法减少机械振动
2. 运动机构维护
(1)直线导轨每月补充专用润滑脂
(2)同步带张力保持60-80N范围内
(3)伺服电机每周检查编码器连接状态
四、工艺参数匹配
1. 材料预处理
(1)高反材料表面喷涂0.05-0.1mm黑化涂层
(2)搭接间隙控制在材料厚度的5%以内
(3)焊接前进行60-80℃预热(针对高碳钢等材料)
2. 保护气体优化
(1)氩气流量15-20L/min(薄板),20-25L/min(厚板)
(2)采用双层气体保护:内层氦气+外层氮气(针对钛合金)
(3)喷嘴距离工件表面保持3-5mm最佳距离
五、智能控制技术应用
1. 实时监控系统
(1)安装熔池监控摄像头(帧率≥1000fps)
(2)配置SPC过程控制系统,设置焊接速度自动调节模块
(3)集成温度反馈系统,动态调节功率和速度
2. 路径规划优化
(1)采用蚁群算法优化焊接路径,减少空行程
(2)复杂轮廓使用小线段平滑处理技术
(3)多层焊接时采用交替扫描策略
注意事项:
1. 每次参数调整后需进行金相检测,确保熔深达到要求
2. 速度提升后要增加焊缝拉力测试频次(建议每10件抽检)
3. 定期进行设备综合效率(OEE)分析,平衡速度与质量的关系
4. 建立参数变更记录制度,保存每次调整的详细数据
通过上述多维度的系统优化,通常可将焊接速度提升30-50%,同时应配合设备预防性维护计划(建议每月8小时全面保养),使设备持续保持最佳工作状态。建议在实施优化前进行DOE实验设计,通过正交试验法确定最优参数组合。
点击右侧按钮,了解更多激光打标机报价方案。
相关推荐
激光焊接机速度慢如何调快点
激光焊接机速度慢如何调快点
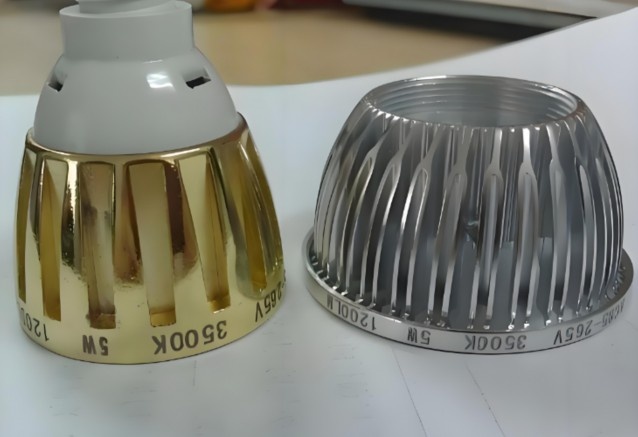
激光焊接机速度慢的优化调整方法
激光焊接机作为精密加工设备,其工作效率直接影响生产效益。当出现焊接速度过慢时,需从设备参数、机械系统、工艺参数等多维度进行系统排查和优化。以下是专业技术人员常用的8大调整策略:
1. 激光功率参数优化
(1)检测激光器实际输出功率,确认是否达到额定值的95%以上
(2)逐步提升功率5%-10%,观察熔深变化,确保不超过材料承受极限
(3)对于连续焊接模式,建议功率密度保持在1×10^5~1×10^6 W/cm²范围
(4)定期校准功率计,每季度进行衰减测试,功率衰减超过15%需更换激光源
2. 动态参数匹配调整
(1)脉冲频率调节:将频率从常规200Hz提升至300-500Hz,需同步缩短脉宽至0.5-2ms
(2)优化离焦量:正离焦量增加熔宽,负离焦量提高熔深,建议调整范围±2mm
(3)波形控制:对高反射材料采用前缓后陡波形,降低飞溅率15%-20%
3. 运动系统升级
(1)将普通步进电机更换为闭环伺服电机,定位精度提升至±0.01mm
(2)采用直线电机驱动,加速度可达5g,速度提升至10m/min
(3)使用轻量化焊接头,质量减轻40%可提升动态响应速度
4. 光路系统维护
(1)每日检查聚焦镜污染度,透光率低于90%立即更换
(2)季度性校准光路同轴度,偏差控制在0.05mm以内
(3)采用可变焦焊接头,实现0.1s级动态调焦
5. 工艺路径优化
(1)运用蚁群算法优化焊接路径,减少空行程30%-50%
(2)复杂轨迹采用样条插补代替直线插补,速度提升20%
(3)开发多层焊接策略,在保证质量前提下减少焊接道次
6. 辅助系统改进
(1)气体流量优化:铝合金焊接时氩气流量控制在15-25L/min
(2)采用双气路设计,前气路防氧化,后气路加速冷却
(3)升级水冷系统,确保水温波动≤±1℃
7. 材料预处理技术
(1)对高反材料实施喷砂处理,吸收率提升40%-60%
(2)预置0.1-0.3mm间隙,可提高焊接速度15%以上
(3)使用活性剂(如TiO2),降低熔池表面张力
8. 智能控制系统应用
(1)加装熔池监测系统,实时调整参数
(2)采用机器学习算法,建立工艺参数数据库
(3)实施数字孪生技术,预判最优焊接参数
安全注意事项:
1. 每次参数调整幅度不超过10%
2. 速度提升后需进行金相检测
3. 定期进行设备预防性维护
4. 修改参数后执行试焊程序
建议采取PDCA循环优化模式:计划(Plan)-执行(Do)-检查(Check)-处理(Act)。每次调整后使用高速摄像机(≥5000fps)记录焊接过程,结合焊缝渗透检测、拉力测试等质量验证手段,建立参数优化矩阵表。通过系统化调整,通常可将焊接速度提升30%-50%,同时保证焊缝强度不低于母材的85%。对于特殊材料或复杂工况,建议联系设备厂商进行深度参数整定。
点击右侧按钮,了解更多激光打标机报价方案。
激光焊接机怎么调试
激光焊接机怎么调试
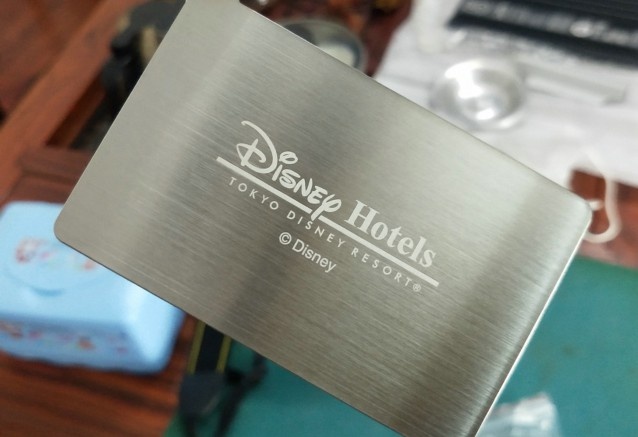
激光焊接机的调试是确保焊接质量、提升设备效率的关键环节。以下是激光焊接机调试的详细步骤和注意事项,内容涵盖设备检查、参数设置、试焊优化等关键环节:
一、调试前的准备工作
1. 设备检查
– 硬件检查:确认激光器、振镜/焊接头、冷却系统、气路(保护气体)等组件连接正常,无松动或损坏。
– 电源与接地:检查电源电压稳定性,确保设备接地良好,避免电磁干扰或漏电风险。
– 光路清洁:使用无尘布清洁激光输出窗口、聚焦镜片,避免灰尘影响光束质量。
2. 环境要求
– 工作区域需保持干燥、通风,避免金属粉尘或油污污染光学元件。
– 温度控制在15~30℃,湿度低于60%,防止激光器因过热或结露故障。
二、核心参数设置与校准
1. 光路校准
– 红光定位校准:开启指示红光,调整振镜或焊接头位置,确保激光束与工件表面垂直。
– 焦点位置确定:使用不锈钢试片进行打点测试,通过烧蚀痕迹判断焦点位置。正离焦(焦点在工件上方)常用于深熔焊,负离焦(焦点在工件内部)适用于热传导焊。
2. 参数初步设置
– 功率与速度:根据材料厚度和类型选择基础参数。例如,焊接0.5mm不锈钢时,功率建议300~500W,速度40~80mm/s。
– 脉冲频率(连续/脉冲模式):薄板材料可选用高频脉冲(如200Hz)以减少热输入;厚板使用连续波模式。
– 保护气体设置:氩气或氮气流量通常为10~20L/min,喷嘴距离工件5~10mm,角度倾斜15°~30°。
三、试焊与参数优化
1. 试焊操作
– 使用与量产材料相同的试片进行焊接,观察焊缝成型效果。
– 关键指标:检查焊缝宽度、熔深、表面光滑度,以及是否有气孔、裂纹等缺陷。
2. 参数动态调整
– 功率调整:若熔深不足,可逐步提升功率(每次增加5%~10%);若烧穿则降低功率。
– 速度优化:速度过快会导致焊缝不连续,过慢则热影响区扩大。通过试焊找到速度与熔深的平衡点。
– 离焦量修正:调整离焦量(±0.2mm微调)可改变能量密度,优化焊缝形貌。
四、常见问题与解决方法
1. 焊缝不均匀
– 检查光路是否偏移,重新校准振镜或聚焦镜。
– 确认工件装夹平整,避免间隙或翘曲导致能量分布不均。
2. 气孔或飞溅
– 提高保护气体纯度(99.99%以上),调整气体流量或喷嘴角度。
– 降低功率或提高焊接速度,减少熔池沸腾。
3. 设备报警
– 水温报警:检查冷却系统是否堵塞,确保水温在25℃以下。
– 光闸异常:清理激光路径障碍物,复位安全开关。
五、安全与维护
1. 安全防护
– 操作时佩戴激光防护眼镜,避免直视光束或反射光。
– 设置安全光栅或围栏,防止非工作人员进入作业区。
2. 日常维护
– 每日清洁光学元件,每月检测激光器输出功率稳定性。
– 定期更换冷却水(建议使用去离子水),每季度润滑机械运动部件。
六、调试记录与标准化
– 记录每次调试的参数组合及焊接效果,建立工艺数据库。
– 对合格参数进行标准化,编写操作手册,便于快速切换不同产品。
通过系统化的调试流程,可显著提升激光焊接机的加工精度与稳定性。需注意,不同品牌、型号的设备可能存在差异,调试时应结合厂家技术手册灵活调整。实际生产中还需通过金相检测、拉力测试等验证焊接质量,持续优化工艺参数。
点击右侧按钮,了解更多激光打标机报价方案。
激光焊接机怎么调焊点大小
激光焊接机怎么调焊点大小
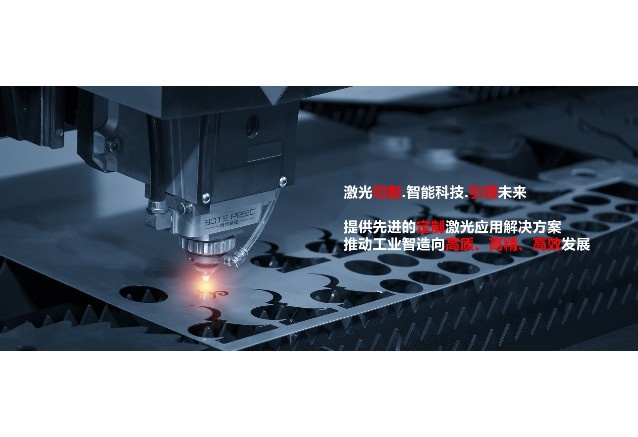
激光焊接机的焊点大小直接影响焊接强度、热影响区范围以及产品外观质量。要精准调控焊点尺寸,需从设备参数、光学系统和工艺条件三方面进行系统性优化。以下是专业工程师常用的六种核心调整方法:
一、激光功率的精细调控
1. 基础功率设定:功率与焊点直径呈正相关,304不锈钢焊接时,功率每增加100W,熔池宽度约扩大0.1-0.3mm
2. 动态功率控制:薄板焊接(<0.5mm)采用脉冲调制,峰值功率与基值功率比建议3:1,可减少热累积 3. 功率渐变策略:在焊缝起止端设置10%功率斜坡,避免出现弹坑效应 二、光斑直径的精确控制 1. 聚焦镜选择:采用F-theta透镜时,焦距每增加50mm,焦点光斑直径增大15-20μm 2. 离焦量调节:正离焦(+0.5mm)可使光斑直径扩大30%,负离焦(-0.3mm)提高能量密度 3. 振镜扫描技术:通过改变扫描路径(螺旋形/线形),实现0.2-2.5mm范围内的焊点调控 三、时间参数的优化组合 1. 脉冲频率匹配:200Hz高频脉冲适合0.3mm以下微焊点,50Hz低频用于深熔焊 2. 脉宽调节法则:铜合金焊接时,将脉宽从2ms增至5ms,焊点直径可扩大40% 3. 占空比控制:保持15-30%占空比可平衡熔深与热输入 四、辅助工艺参数的协同 1. 保护气体优化:氩气流量8-12L/min时,熔池表面张力降低15%,有利于焊点成形 2. 焊接速度调控:速度每提升0.5m/min,焊点长度缩短20%,但需保持功率速度比恒定 3. 多道焊策略:对3mm以上厚板,采用40%重叠率的蛇形路径焊接 五、材料特性的适配调整 1. 反射率补偿:铝合金焊接时需预设功率上浮20%,并采用蓝光激光或光束摆动 2. 热传导适配:铜材焊接推荐使用500ns短脉冲,配合0.2mm离焦量 3. 表面处理要求:氧化层厚度超过5μm时,需先进行等离子清洗 六、智能调控技术应用 1. 闭环控制系统:配备CCD视觉传感器,实时监测熔池直径,精度可达±5μm 2. 人工智能算法:基于深度学习的参数预测模型,可减少80%的试错成本 3. 数字孪生技术:通过虚拟仿真预判焊点形貌,准确率超过92% 注意事项: 1. 每次参数调整后需进行金相检测,确保熔深达到板厚的1/3-1/2 2. 高反材料焊接时,需定期检查保护镜片,反射率超过30%应立即更换 3. 建立参数组合数据库,按材料厚度分类存储优化方案 建议采用正交试验法进行参数优化,先固定功率和速度,以离焦量和脉冲频率为变量,通过9组基础实验建立响应面模型。实际操作中推荐配备红外热像仪监测温度场分布,确保热输入量控制在材料相变临界值以下。定期使用标准试片进行设备能力验证,保证工艺稳定性。
点击右侧按钮,了解更多激光打标机报价方案。
免责声明
本文内容通过AI工具智能整合而成,仅供参考,博特激光不对内容的真实、准确或完整作任何形式的承诺。如有任何问题或意见,您可以通过联系1224598712@qq.com进行反馈,博特激光科技收到您的反馈后将及时答复和处理。