视觉定位激光打标机使用方法
以下是关于视觉定位激光打标机使用方法的详细指南,约800字:
一、设备概述与原理
视觉定位激光打标机是一种结合高精度视觉识别与激光加工技术的自动化设备,广泛应用于电子元件、五金工具、医疗器械等领域的精密打标。其核心原理是通过工业相机对工件进行图像采集,软件自动分析定位后,由激光器在预设位置完成打标。相比传统设备,视觉定位功能显著提升了复杂工件的加工效率和精度。
二、操作前准备
1. 环境检查
– 确保设备放置在平稳、无振动的台面,避免阳光直射或粉尘环境。
– 检查电源电压稳定(通常为220V±10%),接地良好。
– 激光器冷却系统(如水冷机)需提前启动,确保温度在20-25℃。
2. 设备组装
– 安装激光振镜头,调整焦距至标准值(参考设备说明书)。
– 连接视觉相机并校准镜头角度,确保视野覆盖工件加工区域。
3. 软件配置
– 安装配套控制软件(如EzCad、MarkingMate等),导入设备驱动。
– 设置相机参数(分辨率、曝光时间)以适应不同材质反光特性。
三、操作流程
步骤1:工件定位与视觉校准
1. 将待加工工件固定在载物台上,确保无偏移或松动。
2. 启动视觉定位系统,通过软件触发相机拍摄工件图像。
3. 使用软件工具(如模板匹配、特征点识别)标定工件的基准位置。若工件为批量加工,需设定“定位基准点”实现自动追踪。
步骤2:参数设置
1. 激光参数
– 根据材料类型(金属/塑料/玻璃等)调整功率(20%-100%)、频率(20-80kHz)、速度(100-2000mm/s)。
– 示例:不锈钢深雕建议功率80%、频率50kHz、速度300mm/s。
2. 打标内容设计
– 导入矢量图(DXF/AI格式)或直接输入文字,调整尺寸、旋转角度。
– 启用“自动填充”功能优化复杂图案的雕刻效果。
步骤3:试打标与修正
1. 选择“模拟打标”模式预览路径,确认无超范围误差。
2. 执行单次打标,检查图案清晰度与位置精度。
3. 若存在偏移,通过软件“坐标补偿”功能微调X/Y轴偏移量(通常±0.05mm)。
步骤4:批量加工
1. 启用“自动连续加工”模式,设置工件间隔时间(如2秒/个)。
2. 监控加工过程,确保视觉系统实时校正位置偏差。
四、安全与维护
1. 安全规范
– 操作时佩戴防护眼镜,禁止直视激光光束。
– 加工易燃材料时开启排烟系统,避免烟雾聚集。
2. 日常维护
– 每日清洁镜头与振镜表面(使用无尘布+无水乙醇)。
– 每月检查光路准直度,校准激光输出功率。
– 每季度润滑传动导轨,更换冷却水(水冷机型)。
五、常见问题处理
1. 定位偏移
– 原因:基准点模糊或相机镜头污染。
– 解决:清洁工件表面油污,重新标定基准。
2. 打标不清晰
– 原因:激光功率不足或焦距错误。
– 解决:提高功率10%-20%,调整Z轴高度。
3. 软件报错
– 原因:通信中断或硬件过热。
– 解决:重启设备,检查USB/网线连接,确认散热正常。
六、总结
视觉定位激光打标机通过智能化操作大幅提升了加工效率,但需严格遵循操作流程与安全规范。建议定期参加厂商培训,并记录每次参数调整数据以优化长期使用体验。
以上内容约800字,涵盖设备使用全流程及注意事项,可根据实际机型细节进行补充调整。
点击右侧按钮,了解更多激光打标机报价方案。
相关推荐
激光打标机定位技巧
激光打标机定位技巧
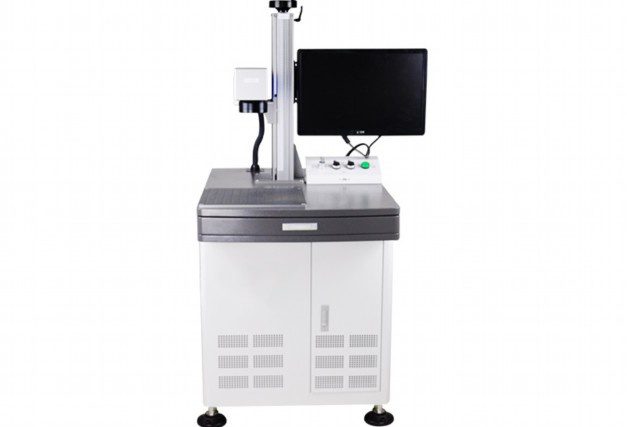
激光打标机精确定位技术全解析
激光打标机作为现代精密加工的核心设备,其定位精度直接影响产品标识质量和加工效率。本文系统阐述激光打标机的定位技术要点,结合实践案例解析关键操作技巧,为工程技术人员提供专业指导。
一、定位系统的核心原理
激光打标机的定位精度由光机电协同系统共同保证。激光器发射的1064nm波长光束通过振镜系统进行X-Y轴偏转,配合F-theta透镜组实现平面聚焦。精密伺服电机驱动振镜的角位移精度可达0.001°,配合200mm焦距镜头时,理论定位精度达±5μm。但在实际应用中,机械振动、热变形等因素会导致误差放大,需通过多重技术手段进行补偿。
现代设备普遍采用闭环控制系统,通过编码器实时反馈振镜位置,配合PID算法动态调整驱动电流。某品牌设备实测数据显示,闭环控制可使重复定位精度提升至±2μm,较开环系统提升60%。
二、四维定位技术体系
机械定位法适用于批量加工标准化产品,采用精密夹具配合定位销实现工件固定。某汽车零部件企业采用真空吸附平台配合机械限位块,将直径50mm的轴承套圈定位误差控制在±0.02mm以内。注意定期校准平台平面度,建议每月使用激光干涉仪检测,平面度偏差超过5μm需及时调整。
视觉定位系统通过CCD相机捕捉工件特征点,采用SIFT算法进行图像匹配。某电子元件制造商在加工手机SIM卡槽时,采用500万像素工业相机配合环形光源,实现0.01mm级定位精度。建议设置图像采集与激光加工的延时参数,补偿机械运动滞后。
激光定位技术包含红光辅助定位和飞行光路标定。在PCB板打标中,采用635nm红光预扫描定位,通过对比实际光斑与预设坐标的偏差,自动生成补偿矩阵。某案例显示,经三次迭代补偿后,500×500mm加工区域的累积误差从0.15mm降至0.03mm。
软件定位方案通过工艺数据库实现智能补偿。某医疗器械企业建立材料-参数映射表,针对钛合金、PEEK等不同材料预设热变形补偿系数。加工3mm厚钛合金标牌时,Z轴自动补偿0.08mm,有效消除热透镜效应导致的焦点偏移。
三、精度提升关键措施
环境温度波动是影响定位精度的首要因素。建议配置恒温车间,温度控制在22±1℃,湿度40-60%。某精密模具企业在车间安装风冷空调系统后,季度设备校准频次由每周1次降至每月1次。
日常维护应重点关注振镜轴承润滑和光路清洁。使用无水乙醇每月清洁扩束镜和聚焦镜,振镜轴承每2000小时补充专用润滑脂。某半导体封装企业统计显示,规范维护可使设备MTBF延长至8000小时。
参数优化方面,建议采用渐进式调试法。先以低速(800mm/s)进行基准测试,逐步提升至设计速度(2000mm/s),同步调整加速度曲线。某金属标牌加工案例中,经参数优化后加工效率提升30%,边缘毛刺减少75%。
针对常见定位异常,反光材料建议采用环形光照明+偏振滤光片组合,某铝材加工企业应用后图像识别成功率从78%提升至95%。曲面工件推荐使用3D动态聚焦系统,某卫浴企业加工弧面龙头时,采用Z轴随动控制将字符变形率控制在0.5%以内。
通过系统化的定位技术应用,某汽车零部件供应商将产品不良率从1.2%降至0.15%,年度质量成本节省超200万元。实践证明,精准定位不仅是技术问题,更是系统工程,需要从设备选型、工艺设计到操作维护的全流程管控。随着机器视觉和AI补偿算法的发展,激光打标定位精度有望突破微米级瓶颈,开启精密制造新纪元。
点击右侧按钮,了解更多激光打标机报价方案。
激光打标机怎么对位置
激光打标机怎么对位置
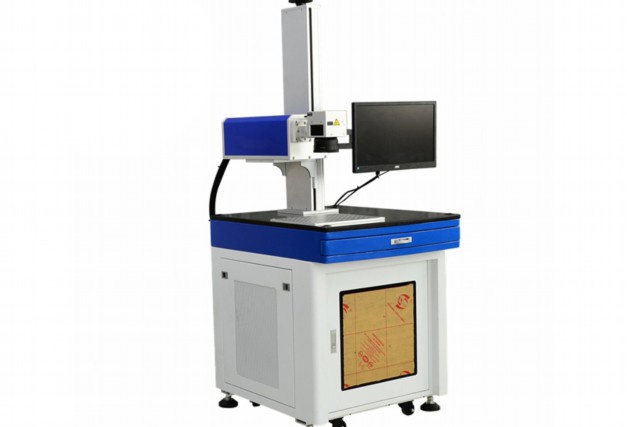
以下是关于激光打标机对位操作的详细指南,共分为六个部分,约800字:
一、激光打标机对位的重要性
激光打标机的对位是确保加工精度的核心步骤。精确对位能避免图案偏移、模糊或尺寸误差,直接影响产品质量。对位过程需结合硬件调整与软件校准,需耐心操作。
二、对位前的准备工作
1. 设备检查
– 确认激光头、振镜、工作台无松动或损坏。
– 清洁镜头与工件表面,避免灰尘影响定位。
2. 安装夹具
– 根据工件形状选择磁性夹具、真空吸附台或机械卡具,确保固定稳固。
3. 参数预设
– 在控制软件中预设材料类型、功率、速度等基础参数。
三、基础对位操作步骤
1. 焦点校准
– 红光定位法:开启红光指示功能,调整Z轴使红点最小(即焦点位置)。金属材料通常焦距为10-15cm,非金属可能更短。
– 试刻法:在废料上打标简单图形,观察清晰度,微调Z轴直至线条锐利。
2. 坐标系设定
– 原点设置:将激光头移动到工件起始点,在软件中设为(0,0)。
– 工件坐标系:输入实际加工尺寸,确保软件坐标与实物匹配。
3. 振镜校准
– 使用校准板(带标准十字线或网格),通过软件执行自动校正,补偿X/Y轴偏差。
四、进阶对位技巧
1. 视觉辅助定位
– 配备CCD相机的机型可拍摄工件图像,通过软件叠加虚拟标线精准对齐。
2. 分层对位法
– 对曲面工件,分段调整Z轴高度,保持焦点在不同区域的一致性。
3. 多点标定
– 在工件四角打标参考点,测量实际距离并修正软件参数。
五、常见问题与解决方案
| 问题现象 | 可能原因 | 解决方法 |
|-|||
| 图案偏移 | 原点设置错误 | 重新设定原点并锁定夹具 |
| 局部模糊 | 焦距不准或台面不平 | 调整Z轴高度/使用调平仪 |
| 重复定位精度差 | 导轨磨损或电机失步 | 清洁导轨/检查驱动器参数 |
| 红光与实际偏差大 | 光路偏移 | 重新校准振镜或调整反射镜角度 |
六、注意事项
1. 安全防护:佩戴护目镜,避免激光直射或反射光伤眼。
2. 环境控制:保持室温20-25℃,湿度40-60%,防止热胀冷缩影响精度。
3. 定期维护:每月清洁光路系统,每季度校验振镜参数。
4. 文件备份:保存常用材料的对位参数,提升后续作业效率。
通过以上步骤的系统操作,可显著提升激光打标机的定位精度。建议首次操作时使用废料反复测试,熟练掌握后再进行正式加工。不同机型细节可能略有差异,具体操作请参考设备说明书或联系厂家技术支持。
点击右侧按钮,了解更多激光打标机报价方案。
激光打标机打位图教程
激光打标机打位图教程
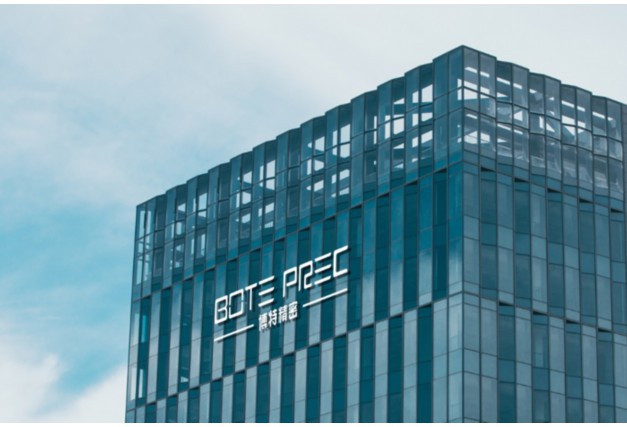
以下是激光打标机操作位图打标的详细教程,内容涵盖关键步骤与注意事项:
激光打标机位图打标操作指南
激光打标机通过高精度激光在材料表面雕刻图案,适用于金属、塑料、木材等多种材质。位图打标(又称点阵打标)需将图片转换为黑白或灰度模式后加工,操作流程如下:
一、前期准备
1. 设备检查
– 确认激光器、振镜、聚焦镜清洁无尘。
– 检查冷却系统(水冷/风冷)是否正常运作。
– 固定材料并调整工作台高度,确保焦点对准。
2. 图片处理
– 选择图片:优先使用高对比度、线条清晰的图像(如Logo、文字)。
– 分辨率调整:建议300-600 DPI,过低会导致锯齿,过高可能延长加工时间。
– 格式转换:
– 使用Photoshop或CorelDRAW将图片转为BMP或PNG格式。
– 灰度模式:通过”图像→模式→灰度”调整层次感。
– 二值化处理:阈值控制在120-180(根据图片明暗调节)。
二、软件设置
1. 导入图片
– 打开激光打标软件(如EzCad、LaserMark),点击”文件→导入位图”。
– 勾选”反色”选项(部分软件需反转颜色以匹配打标效果)。
2. 参数配置
– 打标参数:
– 功率:金属材质建议20-60%,非金属材质5-30%(具体视材料厚度调整)。
– 速度:500-3000 mm/s(速度越慢颜色越深)。
– 频率:20-80 kHz(高频适合精细图案)。
– DPI设置:与图片分辨率匹配,通常设为500-1000 DPI。
– 填充模式:选择”双向扫描”提升效率,复杂图案用”单向扫描”减少错位。
3. 尺寸定位
– 拖动软件中的图像框调整打标区域大小。
– 使用”红光预览”功能确认打标位置,避免材料浪费。
三、打标测试与优化
1. 试打样
– 在边角料或同材质废料上进行小范围测试。
– 观察效果:过浅则提高功率/降低速度,过深或烧焦则反向调整。
2. 进阶优化
– 分层打标:对深浅区域设置不同参数,增强立体感。
– 抖动算法:开启软件中的”误差扩散”模式,减少阶梯状边缘。
– 抗锯齿处理:平滑图像轮廓,尤其适用于弧形或斜线。
四、正式打标与收尾
1. 启动加工
– 关闭设备舱门,启动激光打标程序。
– 实时观察打标过程,遇异常立即暂停。
2. 效果检查
– 用软毛刷清理表面残渣,避免划伤。
– 对比设计图,检查细节是否完整(如小文字、细线条)。
3. 设备维护
– 清理工作台碎屑,用无水酒精擦拭镜片。
– 记录本次参数,建立材料-参数对照表供后续参考。
注意事项
1. 深色材料打标时需降低功率,防止过度碳化。
2. 透明/反光材料(如玻璃)需先喷涂打标涂层。
3. 连续工作2小时后关闭激光器休息10分钟,延长使用寿命。
4. 复杂图案建议分区域打标,避免热累积导致变形。
通过以上步骤,可高效完成位图打标任务。不同设备型号操作细节或有差异,建议结合设备说明书灵活调整参数。掌握原理后,可尝试渐变、3D浮雕等进阶玩法,充分发挥激光打标机的创意潜力。
点击右侧按钮,了解更多激光打标机报价方案。
免责声明
本文内容通过AI工具智能整合而成,仅供参考,博特激光不对内容的真实、准确或完整作任何形式的承诺。如有任何问题或意见,您可以通过联系1224598712@qq.com进行反馈,博特激光科技收到您的反馈后将及时答复和处理。