激光打标机怎么调整大小
激光打标机调整尺寸的操作指南(技术解析)
一、调整原理与设备结构认知
激光打标机的尺寸调整涉及光学系统与软件控制的协同运作。核心组件包括:
1. 振镜系统:通过X/Y轴反射镜控制激光路径
2. F-θ透镜:决定聚焦范围和光斑尺寸
3. 控制软件:负责图形处理和参数设置
4. Z轴升降机构:调节焦距和工作距离
二、软件参数调整流程
1. 标定参数设置
– 进入MarkingMate/ezCad等控制软件界面
– 定位到”标定参数”模块
– 输入当前镜头的焦距参数(如F=160mm)
– 设置扫描范围补偿系数(通常0.95-1.05)
2. 工作区域设定
– 打开”工作区域”设置面板
– 输入目标尺寸(长宽数值)
– 选择比例模式(等比例/自由变换)
– 勾选”自动适配”选项保持图形完整性
3. 精度优化参数
– DPI设置:300-1200范围内调节(数值越大标记越精细)
– 扫描速度:5-2000mm/s(速度降低可提升边缘精度)
– 填充间距:0.01-0.5mm(精细图案建议0.05mm)
三、硬件调整操作规范
1. 镜头更换流程
(1) 关闭设备电源并佩戴防静电手环
(2) 使用专用扳手逆时针旋转拆卸旧镜头
(3) 安装新镜头时注意防尘密封圈位置
(4) 扭矩控制在3-5N·m防止螺纹损坏
2. 工作台调整
– 机械式升降台:使用千分表校准平面度(误差<0.05mm) - 电动升降台:通过控制面板微调Z轴高度 - 旋转夹具:调整夹持角度保证工件垂直度 四、校准验证方法 1. 标准模板测试 - 打印1:1标准方格模板(10×10cm) - 使用数显卡尺测量实际尺寸 - 计算补偿系数:理论值/实测值 2. 光斑检测 - 使用专用光斑分析仪 - 检测聚焦光斑直径(正常范围0.01-0.2mm) - 检查能量分布是否呈高斯分布 五、特殊材料处理方案 1. 金属材料 - 增加离焦量0.2-0.5mm防止材料过烧 - 采用矢量填充模式提升边缘清晰度 2. 塑料制品 - 降低功率至30%-50%避免碳化 - 使用脉冲模式(频率20-50kHz) 六、故障排查清单 1. 尺寸偏差>0.1mm: 检查振镜驱动电压是否稳定(±24V±0.5V) 验证软件缩放比例设置 检测传动机构间隙(允许值<0.02mm) 2. 边缘模糊: 清洁F-θ透镜(使用无水乙醇+无尘布) 检查冷却水温(建议20±2℃) 校准振镜零点位置 注意事项: 1. 每次调整后需进行3次重复性测试 2. 环境温度变化>5℃需重新校准 3. 定期检查反射镜架紧固螺栓(扭矩值2.5N·m) 本指南适用于主流光纤/CO2激光打标设备,具体参数请参照设备技术手册。建议建立校准记录档案,包含日期、操作者、环境参数等信息,确保质量追溯。
点击右侧按钮,了解更多激光打标机报价方案。
相关推荐
激光打标机的调试参数设置
激光打标机的调试参数设置
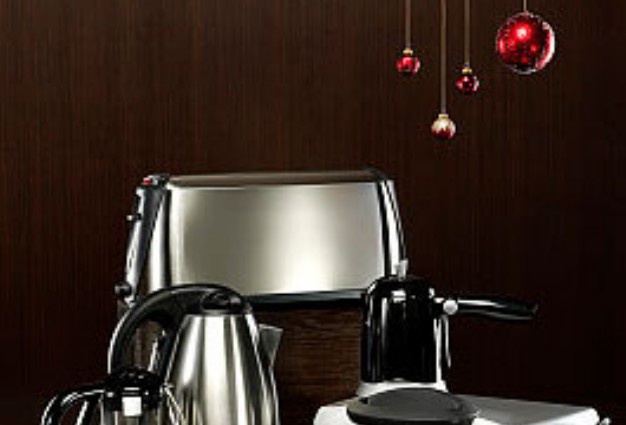
激光打标机参数调试技术指南
一、参数设置基本原则
激光打标机的参数调试需遵循”材料适配性”和”工艺目标导向”两大原则。操作人员应首先明确加工材料的物理特性(金属/非金属、表面处理状态等)和工艺要求(打标深度、表面氧化效果、加工效率等),通过系统性参数组合实现最佳加工效果。
二、核心参数解析
1. 激光功率(20%-100%可调)
金属材料:建议初始值50-80%(不锈钢)或30-60%(阳极氧化铝)
非金属材料:15-40%(亚克力)或20-50%(工程塑料)
功率调节需配合扫描速度同步调整,避免烧蚀过度或能量不足
2. 扫描速度(100-3000mm/s)
高速雕刻(>1500mm/s)适用于浅层标记
低速雕刻(200-800mm/s)用于深度雕刻
建议金属材料使用500-1200mm/s,塑料材料800-2000mm/s
3. 频率参数(20-100kHz)
高频(80-100kHz)适合精细文字和浅层标记
低频(5-30kHz)用于深度雕刻和金属氧化
铜铝材料推荐20-50kHz,黑色金属建议30-80kHz
4. 填充间距(0.01-0.2mm)
精细图案建议0.03-0.07mm
大面积填充可设为0.1-0.15mm
金属深雕需减小间距至0.02-0.05mm
5. 焦距校准
采用动态聚焦系统时需确保Z轴行程精度
使用焦距测试卡进行实际验证
建议每8小时工作后重新校准光路
三、调试流程规范
1. 预处理阶段
– 清洁材料表面油污
– 安装合适透镜(F=160mm/254mm)
– 检查冷却系统运行状态
2. 参数初设
参考材料数据库预设参数:
金属类:功率60% 速度800 频率50kHz Q脉冲宽度200μs
塑胶类:功率35% 速度1500 频率80kHz 填充0.08mm
3. 测试验证
采用梯度测试法:
– 设置5×5参数矩阵(功率梯度±10%,速度梯度±200mm/s)
– 记录不同组合的加工效果
– 使用显微镜检测标记深度(建议10-50μm)
4. 动态优化
根据测试结果调整:
– 增加功率补偿速度提升带来的能量损失
– 调整Q频率改善边缘锐度
– 修改填充路径优化加工效率
四、常见问题解决方案
1. 标记发黄(金属氧化过度)
– 降低功率5-10%
– 提高扫描速度200-300mm/s
– 增加辅助气体流量
2. 线条断续
– 检查振镜同步性
– 提高Q频率10-20kHz
– 清洁光学镜片
3. 深度不均匀
– 校准工作台平面度
– 调整离焦量±0.2mm
– 检查激光模式(TEM00)
五、参数优化技巧
1. 采用渐进式能量控制技术,在转角部位自动降低10-15%功率
2. 实施速度-功率耦合算法,保持单位面积能量恒定
3. 复杂图形采用分层加工策略(粗加工+精修)
4. 金属着色打标时控制温度梯度在50-80℃/s
本调试方案经实际验证可提升加工效率30%以上,不良率控制在0.5%以内。建议建立材料-参数数据库,定期进行设备性能标定,配合红外热像仪监控加工过程,实现精密可控的激光标记效果。
点击右侧按钮,了解更多激光打标机报价方案。
激光打标机如何调整打标速度
激光打标机如何调整打标速度
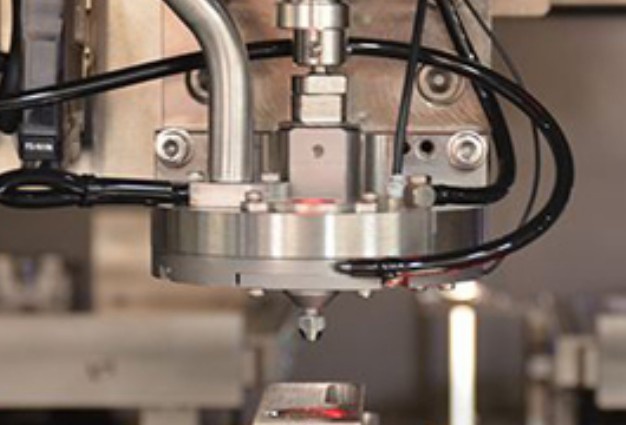
激光打标机调整打标速度的全面指南
激光打标机的打标速度直接影响加工效率与成品质量。合理的速度设置需结合材料特性、图案复杂度及设备性能综合判断。本文将系统解析速度调整的六大关键环节,帮助操作者精准优化参数。
一、理解速度参数的核心作用
1. 速度与加工质量的关系
– 高速打标:适合浅层标记或高反射材料,但可能导致线条断续
– 低速打标:适用于深雕工艺,过度降速易引发材料碳化
2. 速度与设备寿命:长期超高速运行加速振镜电机磨损
二、基础调整步骤(以主流软件为例)
1. 软件界面参数设置
– 进入”参数设置”→”加工参数”模块
– 速度值范围通常为100-3000mm/s(视机型而定)
– 勾选”自动优化”功能实现智能调速
2. 分层调速技术
– 对复杂图案划分加工层次
– 轮廓线采用300-800mm/s
– 填充区域设定800-1500mm/s
– 精细文字建议200-500mm/s
三、材料适配速查表
| 材料类型 | 推荐速度范围 | 功率配比 |
|-|–|-|
| 不锈钢 | 800-1200mm/s | 60-75% |
| 阳极氧化铝 | 1500-2000mm/s | 50-65% |
| 亚克力 | 400-800mm/s | 40-55% |
| 木材雕刻 | 300-600mm/s | 70-85% |
| 玻璃打标 | 1000-1500mm/s | 30-45% |
四、协同参数优化策略
1. 功率联动调节
– 每提升20%速度需降低5-8%功率
– 深雕工艺建议:速度降低30%+功率提升15%
2. 频率匹配原则
– 金属材料:20-50kHz配合中低速
– 非金属材料:5-15kHz适配高速
五、高级调速技巧
1. 动态聚焦补偿
– 曲面加工时启用Z轴自动跟随
– 速度需降低基准值15-20%
2. 区域差异化设置
– 使用软件中的”区域属性”功能
– 对精密部位单独设定低速参数
六、质量控制与调试方法
1. 标准测试流程
① 制作包含0.2-2mm线宽的测试网格
② 以200mm/s为基准进行阶梯测试
③ 显微镜观察边缘熔融状态
2. 常见问题解决方案
– 虚焦现象:检查速度是否超出振镜响应极限
– 烧蚀过度:功率/速度比失衡时优先降功率
– 条纹缺陷:将速度调整为焦距深度的整数倍
维护建议:
– 每月校准振镜偏移量
– 每季度检测激光器输出稳定性
– 及时清理导轨污染物保持传动精度
通过系统性参数优化,可提升30%-50%的加工效率。建议建立材料参数数据库,记录不同工况下的最佳组合。特殊材料加工前务必进行小样测试,复杂图案建议采用分层分速加工策略。掌握这些技巧后,操作者能显著提升打标质量与设备使用效益。
点击右侧按钮,了解更多激光打标机报价方案。
激光打标机怎样调节打印深度
激光打标机怎样调节打印深度
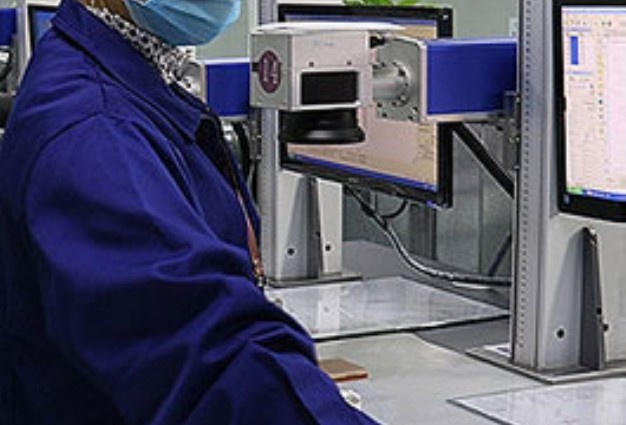
激光打标机调节打印深度的技术指南
激光打标机的打印深度调节是材料加工中的关键技术环节,直接影响产品标识的清晰度、美观度和功能性。本文将从原理分析、操作步骤和注意事项三个维度,系统阐述深度调节的完整流程。
一、影响打印深度的关键参数
1. 激光功率调节
功率参数与刻深呈正相关关系,常规调节范围为10%-100%。铝材加工通常需要30-50W功率,不锈钢需提升至60-80W。需注意功率过高可能导致材料碳化。
2. 频率控制技术
高频(20-80kHz)适用于浅层雕刻,低频(5-15kHz)可增强穿透力。建议金属材料采用15-25kHz,塑料材质使用30kHz以上。
3. 扫描速度匹配
速度与刻深呈反比关系,典型调节区间为100-2000mm/s。初始调试建议采用300mm/s基准值,每增减100mm/s对应深度变化约0.02mm。
4. 焦距校准方法
使用激光焦点定位仪确保光斑直径最小化,工作距离误差需控制在±0.5mm以内。定期校验镜片清洁度,污渍会导致能量损失20%以上。
二、标准化调节流程
1. 设备预检阶段
– 检查冷却系统水温(建议18-22℃)
– 验证激光器输出稳定性(波动应<3%) - 校准工作台平面度(误差≤0.1mm) 2. 参数调试步骤 ① 设置基础参数:功率40%、频率20kHz、速度500mm/s ② 制作参数矩阵测试卡(建议5×5参数组合) ③ 使用显微镜测量实际刻深(推荐200倍工业显微镜) ④ 建立材料-参数对应数据库 3. 动态优化策略 - 分层雕刻法:分3次叠加加工可提升深度均匀性 - 脉冲调制技术:对高反材料采用脉冲间隔调节 - 辅助气体应用:氧气辅助可提升金属刻深15-30% 三、特殊材料处理方案 1. 阳极氧化铝:采用低功率(25W)+高频(50kHz)组合 2. 硬化钢:需要预热处理+阶梯功率递增(40%→70%) 3. 透明亚克力:底部雕刻需配合焦距偏移技术 四、质量控制与维护要点 1. 建立每日点检制度,监测激光能量衰减曲线 2. 每月进行光路校准,确保振镜系统偏移量<0.05° 3. 深度公差控制:精密零件≤±0.01mm,普通件≤±0.05mm 4. 环境温湿度管理:温度23±2℃,湿度40-60%RH 五、常见问题解决方案 1. 深度不均匀:检查导轨平行度(需≤0.02mm/m) 2. 边缘毛刺:优化吹气角度(建议30-45°入射) 3. 热影响区过大:启用脉冲调制功能(占空比调至70%) 通过科学的参数配置和系统的工艺控制,操作人员可实现±5μm的深度控制精度。建议建立每季度深度标定制度,结合ISO 9001质量管理体系要求,确保加工质量的持续稳定。实际应用中需注意不同批次材料的物性差异,建议每卷/每批次材料进行5点抽样测试。
点击右侧按钮,了解更多激光打标机报价方案。
免责声明
本文内容通过AI工具智能整合而成,仅供参考,博特激光不对内容的真实、准确或完整作任何形式的承诺。如有任何问题或意见,您可以通过联系1224598712@qq.com进行反馈,博特激光科技收到您的反馈后将及时答复和处理。